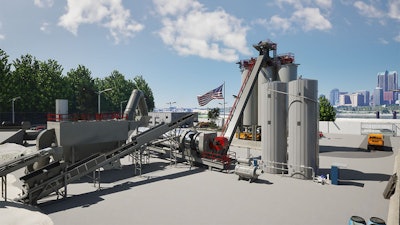
Ammann America’s newest counterflow drum mix plant is now available with a control system designed specifically for the U.S. market.
In addition, the Ammann Alpine DrumMix Plant can now integrate plant production with all other phases of roadbuilding thanks to a new digital tool, the Connected Worksite.
THE CONNECTED WORKSITE
This technology is a suite of software applications that helps businesses plan, control and document the entire construction project, end-to-end (plant to pavement). The Connected Worksite keeps every member of the team fully informed at every stage of the project. It can be utilized for the entirety of a project, or during specific phases:
Construction planning and order management
Customer orders are provided digitally and monitored in real time. Orders can be transmitted as binding or non-binding, which the plant can immediately accept, reject or respond to in more detail. Changes can be made from an office computer or a mobile device from any location. Each instruction is recorded for further review, if needed.
Planning and production at the asphalt plant
The Connected Worksite uses the digital orders to create a production schedule, which is automatically transferred to the plant’s control system. This optimizes material usage and ensures tight deadlines are met. Operating and production data and batch protocols can be analyzed centrally, even if multiple control systems are utilized.
Loading and delivery of materials
As new mix is weighed, the system captures and transmits the appropriate delivery data to the truck driver and the construction team. This allows those at the jobsite to time their work to match the delivery of the mix.
The communication works both ways: The mixing plant receives real-time information about the truck locations, which helps plan further production and loading.
Paving and compaction
Monitoring of mix temperatures is essential to ensuring high quality. With the Connected Worksite, crews know the temperature of the mix at each stage: during production, as it leaves the plant, when it’s in transit, when it arrives, when it’s in the hopper, when it’s behind the screed and during compaction.
Ammann Compaction Expert (ACE), Ammann’s proprietary Intelligent Compaction system, also provides control and guidance. ACE can be supplemented by a cloud-based solution that enables the exchange of information between machines. The data also can be viewed online.
Thorough documentation
Continuous documentation offers valuable insights into all phases. The data helps uncover opportunities for improvement – and at an early stage while adjustments can still be made. At a later date, a detailed history can be shared with clients as needed.
CONTROL SYSTEMS
Two advanced, intuitive control systems are available for the Ammann Alpine. Both seamlessly integrate with the Connected Worksite.
Alpine Smart Control System (ASC)
The new ASC system is a robust, intuitive system developed specifically for the U.S. market. It is a programmable logic controller-based option that has a look and feel that is familiar to operators in the U.S.
Large icons make it easy to see important production functions from across the control room. High-performance graphics screens are color-coded for easy identification. The PLC is provided by Allen-Bradley and designed using off-the-shelf Rockwell Automation software. It is built on Rockwell’s PlantPAX system architecture.
The as1
Ammann also offers the as1 Control System, a highly sophisticated and flexible plant program. The desktop-based solution is extremely popular worldwide; it is in use at more than 3,000 plants around the globe. It has the look and feel of an app from a smartphone or tablet and can effortlessly access numerous productivity modules.
Both the ASC and the as1 can be retrofitted to immediately and cost-effectively improve plant operations. The systems are compatible with plants provided by Ammann or other OEMs.
THE ALPINE DRUMMIX PLANT
The Ammann Alpine is specifically designed for high production and high-capacity recycling technology developed and proven throughout the world. Available in stationary, relocatable, and portable configurations ranging from 300-600 tons per hour, the Ammann Alpine covers all possible plant needs of the American producer.
The Alpine series enables HMA producers to maximize high total production and amount of recycled asphalt (RAP) content without sacrificing mix quality utilizing Ammann’s industry-leading controls and technologies. The Alpine series control system is extremely intuitive and allows tracking and analyzing plant operating data in real time to provide real opportunities to gain further efficiencies over competitive equipment.
High-level benefits of the plant include:
- Single drum, multi-zone drying and mixing system with VFD increases performance and flexibility.
- Modular and scalable designed components
- High RAP capabilities up to 60%
- Warm asphalt capability with the proven Amman Foam system
- Easy customization of plant arrangements
- Easy retrofit to existing facilities
- Extreme wear packages for extended operating life
- 24/7 local support with a hands-on project management team
Ammann’s HMA storage silos have capacities ranging up to 300 tons with extended mix storage options available. Silos are engineered with expansion in mind. The modular silo batcher arrangement is expandable and optimal for retrofitting and matching silo deck heights.
Ammann’s aggregate feed systems include troughing feed belts to eliminate spills, while large bin openings allow for greater capacity. Steep, sloped bin walls optimize material flow, while variable frequency drives promote simple, accurate calibration and production changes on the fly.
The reverse-air baghouse system is the newest version of a broad range of existing Ammann dust control products. The reduced length and increased width of the Alpine series baghouse allows for greater flexibility in accommodating all jobsites and portable requirements.
For more information about the Alpine DrumMix Plant, visit www.ammann.com