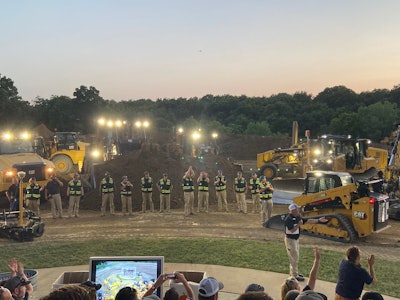
A session on jobsites in the digital age was our first.Lori Ditoro
- Price
- Operators
- Resistance/afraid of change
- It’s the way we've always done it
- Invasion of privacy
- Training
- Having the intention of adopting it but not really implementing it
Among the technology topics discussed during the event were safety and remote control, automation, improved operation and efficiency, sustainability, and simplified use (especially for new operators).
Safety & Cat Command
Some of the most important technology assists with safety and protecting the operators from jobsite and equipment hazards. This includes steep terrain, objects that could be struck and personnel who could be struck.
A demonstration of a Cat Command controlled D5 Dozer; notice that there is no driver in the cabLori Ditoro
Remote operation with Cat Command also eliminates site hazards. Operating near cliff faces or high walls, working on unstable surfaces or steep slopes, or moving hazardous materials can put operators at risk. Even traveling to a remote jobsite poses its own safety issues. Cat Command helps address all these challenges by enabling equipment operators to work outside the machine and, in some cases, miles away from the machine. Cat Command also has an all-stop switched that personnel working on a site with remote vehicles in operation carry. If needed, the stop switch is pressed and all vehicles using Cat Command come to a stop. When conditions are safe, another
A 740 GC articulated dump truck during the demo, loaded using payload indicationLori Ditoro
Operators now work from the company’s headquarters. They can switch between multiple machines in different locations from the same Command Station, in some cases hundreds of miles apart. It keeps operators out of harm’s way. Their moto is “No boots on the barge.” This remote control also opened the labor pool. Blank shared that anyone can operate using remote control, including those with disabilities.
Other Safety Technology
A 325 excavator demonstrates payload indication during the breakout sessions.Lori Ditoro
Some of this technology is specifically around safety:
- Cameras
- Driver safety systems (measuring diver fatigue, distraction events and seatbelt reminders)
- Operator coaching in the cab
Improved Productivity & Efficiency
To improve efficiency and productivity, Caterpillar offers VisionLink (recently updated), which simplifies equipment management. It also improves asset availability while reducing costs for an entire fleet. It offers deep integration with dealer services to ensure alignment on whatever it takes to keep your fleet ready to run. Every eight weeks, a new code automatically goes out to the market.
The recent updates includes the introduction of three new features:
- Cat Grade and Compact
- Operator Coaching
- E-Ticketing
An excavator demonstrates the preciseness of grade control during a breakout session.Lori Ditoro
With Cat grade control and payload indication, rework and repeat tasks are decreased, and accuracy is increased. Grade control allows operators to automatically dig or blade to the correct grade using data uploaded through VisionLink without the need for a USB drive.
With payload indication, operators loading materials into a dump truck, for example, receive automatic weight notifications as they load and the individual loads are added, letting the operator know exactly how much weight is needed for the final delivery to the truck.
Operator Coaching is a VisionLink tool that supports operators across experience levels to enhance their skills. Two categories of operator coaching tips—Operating Efficiency and Machine Health—are tracked. During machine operation, the operator receives an onboard notification when an action with a corresponding tip is detected. This allows operators to strive for continuous improvement in productivity and efficiency while they work.
Sustainability
With emission regulations tightening, the requirement to transition away from diesel is increasing. This change means adding technology to measure battery health and time remaining to work among other capabilities. Expectations are that manufacturers will continue to invest in this and other sustainable technology. The sustainability goals include:
- Reduced carbon footprint
- Decreased fuel burn
- Increased productivity (material moved)
An excavator loads a truck during the demoLori Ditoro
VisionLink also provides data to contractors that assist them in their sustainability goals, including idle time monitoring. Unnecessary idling burns fuel without productive work and should be decreased to as little as possible. Idle monitoring helps with this goal. As described earlier, grade control and payload indication reduces the number of passes or loads required and virtually eliminates rework. Cat Compact allows for intelligent compaction, again reducing passes and rework. All efforts to decrease passes and eliminate rework reduce fuel burn.
Other low-carbon options are biodiesel, hydrotreated vegetable oil and battery electric power. Caterpillar has electric prototypes including a 950GC Medium Wheel Loader. Also, new Caterpillar engines are being designed to operate on low carbon fuels like biodiesel.
Full Automation
There are several challenges for full construction autonomy, and they include:
- Implementation costs
- Dynamic environment
- Process control and keeping people safe around the machine
A D9 dozer during the demoLori Ditoro
Some of this is for the future jobsite, but some automation is already in operation. This includes motion inhibit to prevent collisions. The technology prevents motion until the object is clear. If a machine is in motion, it slows or stops if something is in its path. It also allows the machine to navigate around objects.
Demo Spectacle
At the end of the day as the sun sank below the horizon, the technology team put on a show with equipment and technology surrounding the audience on a rotating grandstand. The audience turned to different areas on the campus to see the technology in action.
About every type and size of equipment was part of the performance. Often at high speed, machines dug, dumped, graded and ripped into the ground in an amazing 360-degree display of power and innovation.