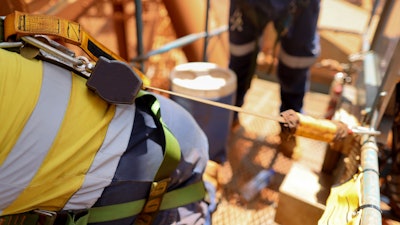
Rental: Can safety hazards be eliminated via engineering and design?
TJ Lyons, Certified Safety Professional Occupational Health and Safety Technologist and Construction Risk Insurance Specialist, of Lyonetics Consulting LLC
Tony Groat, North American Regional Manager at the International Powered Access Federation: Engineering can significantly reduce risk and hazards but it is typically not possible to eliminate hazards entirely. Many potential hazards can be mitigated. This can include using failsafe redundancies, ergonomic considerations, and other safety-first principles. But there are limitations for engineering. There are unintended consequences that also come from some of the designs or protections that actually create another unique set of hazards that need to be taken care of. You do end up having environmental factors that are pretty hard to “engineer” out.
There are technology limitations as well in lots of areas. And there's the bottom line. There's a wide range of availability for design solutions to take place. But when you're looking at the hierarchical solutions, it always leaves areas where other things need to be involved as well.
Kevin Gildea, PE, Product Safety and Compliance Manager at Haulotte: I would agree. I think instead of saying, “design out hazards,” we're more talking about reducing risk to a tolerable level and if it can be reduced even further for some hazards. When you think in a certain context, there's a diminishing return for additional efforts. For example, hydraulic safety. That’s maybe not the area to focus on from a design point of view because it's gotten to the point where the mitigation measures are sufficiently mature. There are other areas that could use additional risk mitigations.
Tony Groat, North American Regional Manager at the International Powered Access Federation
Gildea: Areas that are either new or haven't been explored, or the application of new technology in our industry. Collision avoidance is a good example. LIDAR sensors or different types of sensors that are used in the autonomous vehicle space were, 15 years ago, would be unthinkable to apply them to machines in our industry. Now it's gotten to the point where you could apply them and there are ways to use them.
Brian Clark, Director of Product Support at Sunbelt: Load sense is another example. I've been in the rental industry for over 30 years, and I'm just thinking about how technology has changed over the years. And then we've reduced some hazards in MEWPs over the years. There's always room for improvement as technology changes and as the cost of that technology gets used more. I always equate it to the auto industry. The construction industry as a whole sees what the auto industry does and then, a few years later, tries to implement a similar technology across the board.
Brian Clark, Director of Product Support at Sunbelt
There are a lot of innovations and safety improvements that happened to machinery, mobile machinery that most people wouldn't even be aware of. For instance, the improvements in electronic controllers over the years, where you have much better ability to detect an open circuit or detect that the wrong current is passing through an input. Whereas that was maybe more specialized in the past, but now that's common. There are a lot of improvements that come from other industries that you wouldn't even know as an end user.
Nicholas DeJesse, Assistant Regional Administrator at the Occupational Safety and Health Administration, Region III: I think Tony may have said the one word: ergonomics. I look back, let's say 25 years ago, and ergonomics was an important aspect of what was going on with injuries and illnesses, musculoskeletal disorders, and so on. With that, we came up with the solution, “Let's fit the task to the person, not fit the person to the task.”
One great example, actually, of how design was implemented to help out: we moved certain portions of a [production] line, especially with manual applications. We started doing more in the sense of stretch and flex, lifting procedures, and musculoskeletal risk factors. We've seen a reduction in musculoskeletal disorders over time.
Another great example, and I know this doesn't happen in lifting, but look at our bloodborne pathogens standard and the implementation of engineering devices, to where after an individual an injection—the needle now retracts into the vial itself so now no one could get punctured by that used needle. I think the engineering is out there. But some of the gentlemen actually said, some hazards we can mitigate, or at least, mitigate as low risk as possible. But they are still going to be present. We're still going to have to put in effective controls to ensure people don't get hurt or get killed.
International Powered Access Federation
More from Tony: Can Hazards be Engineered Away?
The question can be misleading within the scope. If the question is implying that ALL hazards can be designed out, engineering can significantly reduce risks and hazards, but it is typically not possible to eliminate all hazards entirely; many potential hazards can be mitigated. This can include using fail-safes, redundancy, ergonomic considerations, and other safety-first design principles.
Limitations of Engineering: Unintended consequences where changes to one aspect of a system might introduce new hazards elsewhere.
Human Factors: Human error can contribute to hazards, and while engineering can mitigate these risks (through training, ergonomics, etc.), it cannot eliminate them entirely.
Environmental Factors: External factors like weather, earthquakes, and other natural events can create hazards that are difficult to engineer against completely.
Complexity: As systems become more complex, the risk of unexpected interactions and failures increases, which can introduce new hazards.
Technological Limitations: The current state of technology might limit the extent to which hazards can be mitigated or eliminated.
Resource Constraints: Budget, time, and other resource constraints can limit the extent to which safety features are implemented.
Rental: On the contractor side of things, how have you seen these ideas affect the jobsite?
Lyons: A great example is in table saws by a company called SawStop…when it touches skin, it shuts off instead of cutting your finger. What we started doing is putting into the contract: “If you're going have a table saw, it's going to have technology that will protect your fingers similar to SawStop.” Rather than waiting for a regulation…you put it in the contract. If it's purchased upfront, you don't have to fight about it later.
Typical of what we've done in the industry is after somebody cuts their finger off, we say “Hey, why don't you use one of the saws that doesn't cut your fingers off?” This is as simple as it gets. If you put in a contract, you eliminate all those conversations about who's going to pay for it, etc. Because it's already put in place. It’s prevention at its best.
Rental: How else has the industry "designed out" hazards?
Groat: I think there's a phenomenal number of those. We talked about overload protection. We ended up having simple things [like] emergency stops, proportional controls, interlocks, self-leveling systems, a full scope of secondary guarding systems, anti-crushing devices, the technology is increased where we now have sensors that will mitigate collisions, accessories are out there like pipe racks that keep people from overloading the guardrails, anti-collision systems, auto-leveling systems on machines.
The list can go on and on. I think that there have been more technological changes in equipment in the last 10 years than probably 20 years prior.
"Over time, machines became more efficient. Not just from the batteries and motors, but from other systems where you had done the work to gain efficiency improvements."
—Kevin Gildea, PE, Product Safety and Compliance Manager at Haulotte
Rental: What are the big safety features of lifting equipment? What are the latest changes?
Clark: One of our larger contractors on large jobsites like data centers and places like that. The most common thing, believe it or not, is simple: perimeter lighting. You're putting lights on the four corners of the MEWP or scissor lift, so you put a visual on the ground so when people are walking around or people are operating the lift they're aware of their surroundings and aware of this, I call it “a bubble of safety,” if you will, around the machines.
It's a growing market. We're renting hundreds and hundreds of these a month. We are working with our suppliers so they have solutions where they can deliver it on the machine integrated with the MEWP.
Groat: What about telematics?
Clark: We're heavily in telematics. For every machine we get today from any manufacturer that offers telematics, we’ll integrate their solution. That helps us with diagnosing problems with the machines. We can see how the operator is using the machines but particularly the machines that have load sense we can see how much weight is in the basket. We can see what's overloaded so if we get a service call like, “Hey, my machine won't raise / my machine won't lower,” we can see [that] they’ve exceeded the 500-lb. capacity, as an example. That technology has helped us with reducing our service calls for sure.
Groat: It seems like a light switch was flipped in regard to moving forward toward full electric machines. Why is that? Is that technology driving that change?
Gildea: There's a lot of reasons. Obviously, there's the environmental side of getting away from fossil fuels. If you have an electric machine, you have a choice of how you're going to get the power to it and it opens things up in the future. The basic building block is an electric machine. If eventually hydrogen fuel cells become common, for example, you need the basic block of having an electric machine in order to get to that. If you want to have it powered by a diesel or a gas engine, you could still do that and that would be another alternative power source. I think that was one of the big drivers.
And then, the benefits that come with having no direct emissions. If you're in an enclosed building, you don’t have to worry about the exposure of fumes while you're working at height.
Another advantage is the controls that go with electric machines. The electronic controls for drive systems have come so far over the years and allow very fine control of movements. Again, that’s a lot driven by the auto industry. I remember 20 years ago, being in a different industry and being a member of SAE (Society of Automotive Engineers)…the continuing education classes were just coming out about designing for hybrid drive trains, and electric motor theory and electric motor controls. They were the first classes that were training engineers on how to work with a non-mechanical drive train. Now it's progressed and you can apply it to our industry because it has this history and background to it.
Clark: We were an early adopter of the JLG’s DaVinci all electrics (scissor lift). Being a fluid-free machine there are some applications for sure that the customers are wanting. We picked up “electrical efficiency” with those machines. Depending on the application, they can go a week without charging—which is another service call from our customers, they don't charge them at night when they leave in the day. A more efficient machine is beneficial for the industry for sure.
"Some hazards we can mitigate, or at least, mitigate as low risk as possible. But they are still going to be present. We're still going to have to put in effective controls to ensure people don't get hurt or get killed."
—Nicholas DeJesse, Assistant Regional Administrator at the Occupational Safety and Health Administration, Region III
Gildea: In general, making the transition from gas and diesel power to electric at first, the battery technology didn't provide the energy storage you needed. OEM’s beat up on hydraulic suppliers, on other components and system suppliers to get more efficient. In the past, you didn't focus on 1 or 2% losses that were coming from your hydraulics for example, but when you were making that transition to electric those small numbers add up and made a difference. Over time, machines became more efficient. Not just from the batteries and motors, but from other systems where you had done the work to gain efficiency improvements.
Clark: I will say there's a movement to go from hydraulic drive to electric drive. We've been a proponent of that for a very long time, we've worked with our manufacturers to ask them to look at this and implement that. That kind of spun out of another manufacturer who was an early adopter. We could see the efficiency—it's hard to calculate—but we could see, the less downtime calls the service calls for batteries.
Gildea: To connect that with reducing or mitigating risks, think about lithium batteries. When those first started to come onto the scene, and they were available for use in our (Haulotte) machines we saw that we could design them in, there was a big focus on safety. They're not like lead acid batteries. There are certain additional safety systems that you need. You need a battery management system (BMS) to monitor Over temperature, Under temperature, Overvoltage, Undervoltage, etc. These are extra safety systems that didn't exist before, that you didn't have to watch before, but are needed because lithium batteries have different risks. I think that's, maybe, one thing that was a big focus on the OEM side and the design side that maybe wasn't as well known to end users or the industry as a whole. That was an area where it was a big effort to mitigate the risks as much as possible by the design of the machine itself.
Lyons: It's being recognized in the field. We're doing work for the Army Corps of Engineers right now and lithium batteries have been added to their manual of special storage containers in construction. Now, typically, they're charged outside of the building, especially wood frame construction. [For example,] we got rid of ladders…because lifts are three times more efficient. But then lifts started traveling off the edge of buildings. So, there are some consequences to the interventions we make.
I did want to add that it's not just the equipment. Let's say a larger company spends 300 work hours putting up a series of piping in a facility, they make that off-site now in a workhouse. They raise this modular assembly in about 4 hours. Not only can we make safer equipment, but we are reducing the excursion hours that we have to do the work at height.
If you build this up on the ground and stick it up into place, and move on to the next building, [that will] dramatically reduce injuries or incidents because they don't have those exposure hours.
DeJesse: I think Tony may have said the one word: ergonomics. I look back 25 years ago, and ergonomics was an important aspect of what was going on with injuries and illnesses, musculoskeletal disorders, and so on. With that, we came up with the solution or saying, “let's fit the task to the person, not fit the person to the task.”
One great example, actually, how design was implemented to help out was that we moved certain portions of a [production] line, especially with manual applications. We started doing more in the sense of stretch and flex, lifting procedures, and musculoskeletal risk factors. We've seen a reduction of musculoskeletal disorders over time.
Another great example, and I know this doesn't happen in lifting, but look at our bloodborne pathogens standard and the implementation of engineering devices, to where after an individual an injection—the needle now retracts into the vial itself so now no one could get punctured by that used needle. I think the engineering is out there. But some of the gentlemen actually said, some hazards we can mitigate, or at least, mitigate as low risk as possible. But they are still going to be present. We're still going to have to put in effective controls to ensure people don't get hurt or get killed.
International Powered Access Federation
"We have a lot of data from our large fleets...working with the manufacturers in the background to make the machine inherently better, which will hopefully make it inherently safer."
—Brian Clark, Director of Product Support at Sunbelt
Rental: Why are not more design solutions seen in the market?
Gildea: I don't wholly agree with the premise that they aren't out there. As mentioned before, there's some design solutions and risk mitigations that are implemented in machines that aren't necessarily apparent to the end user.
Like the lithium battery example. A lot of things were implemented when that technology was used that are definitely improvements, and definitely risk mitigations.
Clark: That's the continuous improvement side of the business. That's not always seen by the end user. We have a lot of data from our large fleets. We work with our manufacturers. We share our breakdowns, our service calls, our details on parts consumption on the machines that are 7 and 8 years old. They're seeing the data from that, and we're working with the manufacturers in the background to make the machine inherently better, which will hopefully make it inherently safer.
Gildea: That's a good point, Brian, anybody that works on machines over the past 20 years knows about the improvements that have been made.
Groat: I have two thoughts on why would be hard to see some things moving along. One of them is the inherent risk of being the first to try something. I know as a buyer of this equipment years ago, you didn't want to be the first one to go out and get the new technology, because there are always bugs with it.
Innovation has cost. Innovation has inherent failures and trying something that you think is going to be the next best thing in the world and it goes over like a lead balloon in the marketplace. There's a lot of cost to innovation—you want to make sure that that innovation is going to be successful. I think the risk to being innovative, can be one area.
Another part of it is sometimes you have a tendency to place the problem in another area of saying that we are not going to address it this way, it should be addressed not through innovation, but through administrative controls. I'll give you an example of one that it's probably the most recent. For years, we ended up having people in the field going over there and putting some type of device across the mid rails to raise their height to get up higher into areas that the guardrails wouldn't allow to get up higher in there. And we kept going, “no, don't do that.” It wasn't till recently that we went over just said, “Why are they doing this” and “How are we going to help them solve that.” Sometimes, I think, we don't necessarily hear or see what the users of this equipment are experiencing and are more reflective on historical approaches: “Don't do that,” “Find a different piece of equipment,” and “Our equipment doesn't do that way.” I think that we're becoming much more innovative as an industry and attuned to that. TJ, I know that you, as contractors, you went over there really tried to look at those things. What are your thoughts?
Lyons: There are two big barriers. Number one is, if you have a fleet of equipment and spent half a million dollars for some of the best scissor lifts in the world 3 years ago, you're not going to buy more scissor lifts even if there's an innovative product out there because you already have scissor lifts.
"An OEM that doesn’t seek to understand the solution and then takes an approach that tries to 'only make the machine as safe as it is required to be for a country' is not in a good position from a liability point of view."
—Kevin Gildea, PE, Product Safety and Compliance Manager at Haulotte
Same problem we had when you move from ladders to scissor lifts. I was in New York once to talk to one of the largest electrical contractors and asked, “How come you’re not using lifts here?” He says, “Oh, we already have the ladders.” Sometimes, I think, our biggest enemy is “it's good enough.”
Number two is blaming the worker for doing something wrong versus the equipment that we put them in that didn't allow him to get to the work. I will guarantee you, and I've seen those things across railings on scissor lifts, we always blame the worker who put them there. We don't look at why he had to do that. It's very unique to the U.S. that we don't look at the condition we put the person in—we look at the person who had to make the decision.
More from Tony: Accessory Approval
I believe MEWP manufacturers are hesitant to approve secondary suppliers' accessories due to safety risks, compatibility issues, liability and legal concerns, warranty and support limitations, regulatory compliance, testing and quality assurance, and brand reputation. By maintaining control over approved accessories, manufacturers can ensure their equipment's safety, reliability, and compliance with industry standards.
Gildea: That's a good point. That's a fertile area to look at. You can't just end the conversation and say “operator error.” without further details. “Operator error” doesn't move safety forward. It is more helpful to understand why that operator’s decision made sense in the context of what the operator knew and their understanding of what the machine was doing as they're trying to do their job. When you define it that way, when you take it beyond operator error, that opens it up to other points to discuss such as “Do you need a different procedure? Do you need a different machine? Do you need a different feature?” You can start to look at specific solutions instead of ending the conversation with “more training” because it may not be knowledge issue.
DeJesse: One thing that I heard over the years, is “what does the standard require.” Until you change this mindset it might be difficult to see more of the innovations—although we've seen many. There may be times where it doesn't seem so opportunistic because people say “What does the standard call for.” If you look at the majority of OSHA standards, most were adopted in the late 1960s They’re baseline or minimal standards. So, until we change the mindset to “we need to be better than the baseline.”
International Powered Access Federation
Rental: Why are not more design solutions supplied as standard on equipment?
Clark: It depends on what you're talking about. Tony mentioned access decks. There's a few manufacturers that have integrated that into the platform as an option but we buy it as a standard. So, the last few years at the manufacturer had it, we include it. It's just that extra piece of safety that's in the machine now. We know that it's not removed. It's not put on another machine where it could be reassembled incorrectly, or something like that. It helped standardize our rental fleet. We know this make, model, and model year all have that access deck. It depends on the customer and the application for everything.
Gildea: Adding to what Brian said, if you look at an innovative improvement that comes to machines or process, there's a lifecycle to it. There's the idea, then typically it's going to be tried on existing machines first. Then it's going to be adopted, maybe, in one geographic area or by one large customer that decides to take a chance on it and has success with it. You gain experience from a lot of different ways. Eventually, it gets refined and reaches the point where you have others working on the same idea. Standards are maybe towards the end.
The problem is that some machines lag behind and people say, “We have a successful solution, we've proven it on existing machines, customers are making it part of tenders and contracts.” Then, why isn't it in the standard and required for every machine?” I think that's the point where the standards push other OEMs, make other users aware of it, and for the people that need that nudge to make it more accepted in the industry and more common.
"If I take the question as 'Why aren't more design solutions made standard as equipment as opposed to accessories,' I’d say what are the drivers to make the change? The first driver would be standards. If you came over and you put in a standard saying, 'This must be on the equipment,' then they're going to be on the equipment. And if they're not, then it becomes a little bit more subjective."
—Tony Groat, North American Regional Manager at the International Powered Access Federation
Lyons: Let me drive into that too, Kevin. Litigation is probably going to drive more of this change than standards, because litigation happens after the incident where standards can take 6-10 years to come through. I appreciate the comments about OSHA, that's even longer to get a standard changed. But, if I'm a consultant and my client has an accident and I'm going to help prepare the case and I knew there was something safer in the field, my opinion would be, “well, if you didn't use this machine, it wouldn't have blown over in the wind because this lift was made to operate in the wind.” Those discussions are ones we rarely have until the attorney calls with a subpoena.
Gildea: That's definitely part of it. I guess what I mean is that before it gets to the standards, some OEM’s have already embraced the idea and the safety early because that's the culture of the company. Or maybe it's required in another country first and then applied in the U.S. But when you get to the point that it is a requirement in the standard, then you're just catching the lagging OEMs.
International Powered Access Federation
Rental: Nicholas, can you comment on how OSHA handles making safety innovations standards?
DeJesse: The federal rulemaking process is a complicated one. I say that based upon a few things. We take into account injury and illness trends. We have advisory committees in all industry sectors, whether construction, general industry or maritime. We discuss what we're seeing in the field. We're always looking at emergent hazards in all these industries as well.
Groat: If I take the question as “Why aren't more design solutions made standard as equipment as opposed to accessories,” I’d say what are the drivers to make the change? The first driver would be standards. If you came over and you put in a standard saying, “This must be on the equipment,” then they're going to be on the equipment. And if they're not, then it becomes a little bit more subjective.
Next, I call it the golden rule. And the golden rule is “the guy with the gold rules.” And generally, that means that the person who is going to be buying the equipment, the big users of the equipment—if they say, “I want this on the equipment” ultimately, the manufacturers are going to put it on the equipment. A good example of that for me was secondary guarding /belly bars. It got to the point where it's not in the standards as a requirement. And a lot of the large users said, “We need something on this equipment” and all of a sudden, one manufacturer went over-made standardized equipment and then everybody else followed shortly after. Sometimes it is the demand of the user saying, “This stuff better be on the equipment” and then it happens.
In a more pragmatic fashion, I would say that MEWPs are used by a wide range of industries, environments, and applications so the requirements for a construction site can be significantly different than a warehouse or a film set. Offering a base model with optional accessories, allows the customer to choose what they want. I think that you don't have to put all the expense on something that may be rarely used, or sometimes can increase some of the impact of fitting those things up.
"We have to be careful with the standards we put in place that we're not putting some of the onus on safety back onto the worker."
—TJ Lyons, Certified Safety Professional Occupational Health and Safety Technologist and Construction Risk Insurance Specialist, of Lyonetics Consulting LLC (retired)
If you look at overload sensors. Some of the guys who were overloading it before, said I'd rather have the old machine than the new one because they weren't concerned about killing a machine that was owned by the rental company. They wanted to put more equipment up in the air, quicker.
There are different drivers that make that happen. Part of it is standards which are going to mandate that everyone's going to do it and if everybody wants that, then that's the driver to make that happen.
Next is the users of the equipment. If they're out there saying they want it, I'm going to say that the manufacturer's obligation is to make sure that takes place. Those are the two greatest drivers, in my opinion, to making accessories standardized.
Rental: Does a safety design solution increase or lower liability?
Lyons: I'm going to go to hard hats. We know helmets unlike hardhats save your life. We don't mandate those, but it's the right thing to do for the individual. The second part of that is it can be a risk to a company that can't afford to upgrade their equipment even though there's a safer way to do it. That's a very tough answer. That's a risk management question they can't answer because they don't have the money to be safer.
Gildea: I think there's a different decision-making approaches of different manufacturers when it comes to liability and whether to make a specific solution Standard or Optional. On the one hand, to make a good decision, you can say you need to understand the pros/cons of the option, the way the machines are used, the requirements in standards/regulations for this country and other countries around the world, what customers are requesting, and what similar safety options are available on the market. In the end, you may say, for example, “We've looked at these options, we've evaluated them and this safety option is better for one application, but it's worse for three other applications so it should be optional” or for solutions that are proven to improve safety for the majority of applications, the decision-making process leads to making a solution standard on every machine.
The decision isn’t always the same but liability becomes less of a concern because the approach to reach that decision was logical and consistent.
On the other hand, an OEM that doesn’t seek to understand the solution and then takes an approach that tries to "only make the machine as safe as it is required to be for a country” is not in a good position from a liability point of view.
DeJesse: From the aspect of what we do or what we see as an agency, it always is going to be the responsibility of the employer to provide a safe and healthy workplace, that includes asking if the person operating the equipment was adequately trained. Are they trained, not only in theory, but also in the sense of safe operation, understanding limitations and expectations of the machinery, and being able to exercise that knowledge in application and use. I would focus on operator training and its effectiveness.
Groat: Does it increase or lower liability? The answer is, yes, it does. It's just that simple.
If you don't have it, you should have had it. If you do have it, did you do all the right things. We talked about things that are not required but they're out there—so why didn't you put them on? And if you have something that you put onto it, did that have contributory issues to the effectiveness of it? Did it mitigate the risk properly? It's like secondary guarding, it’s just that it’s secondary and it’s not going to prevent all crushing incidents.
Even though a solution can mitigate, it doesn't necessarily eliminate everything. I think that there's that issue on the manufacturers in putting a product out there. Was it tested properly? Did you communicate how it's used properly? Even in the user’s application of the device, the integration of it adherence to standards. If you're a user of equipment, why didn't you get that?
I think the issue is that you have both sides like with every risk assessment, you better have gone out there and done your due diligence to assess whether you're mitigating the hazards appropriately or not.
More from Tony: Liability
It can BOTH increase and decrease a manufacturer’s liability.
In general, a design solution’s impact on liability depends on multiple factors, including the design’s effectiveness in mitigating risks, the adherence to safety standards, the communication of safe usage, and how the solution is implemented. A manufacturer’s liability depends on various factors, including safety, testing, documentation, training, design complexity, integration, and adherence to industry standards. By addressing these factors carefully, manufacturers can reduce liability and minimize the risk of legal claims.
Gildea: Tony makes a really good point about being clear about what the option or feature can do. What are the limitations? If you make claims that it's going to protect you in all situations, then that could increase your liability because there's an expectation that it works in a certain way, and it didn't do it. I think you have to be clear; “I have a safety improvement [and] it's good for this situation and this application, and here are the limitations. “
You don't want to not implement an improvement because it doesn’t apply in every situation, there's still benefit even if it's only for some situations.
Lyons: Tied to that Kevin, too, is everybody's listening for “what's in this for me.” As an industry, if we can prove it's faster and more productive and more efficient and not talk about safety, people tend to follow that. People really don't care as much about safety as we'd like to think. It's all about profit and schedule. If we start forming opinions, and I started doing that, working three times faster from a lift than a ladder, people will pay more attention than being told it's a safer thing to do and here's the limitations of it.
International Powered Access Federation
Rental: Why is it difficult to get secondary supplier design solutions approved in this market?
Clark: There's a there's a lot of accessories that are available for all types of MEWPs. With our preferred partners, we would like to have their approval always to use whatever that device is. We don't know if adding a screen around the deck on a boom lift is going to cause any wind drag. We rely on our preferred partners to authorize that solution or come out with their own solution so everybody is aware of the application and it's approval.
Gildea: That's exactly right. I guess, when I hear “approved” from a point of view of an OEM it means: will this change / modification to the machine affect the certification? The safety? Does it affect the assumptions that were made during testing? During design? Analysis?
Can the OEM still stand by the certification and safety of the machine after this modification is added? If yes, then the “approval” can be given.
Rental: How do design solutions affect the user’s perception of safety versus the hazard?
Gildea: I think in some cases, design improvements have progressed to the point where the risk is low enough that it's not something that an operator is going to think about. Take hydraulic safety, for example. We've gotten to the point now where someone is not going to be afraid standing next to a hydraulic manifold or operating machine or a high-pressure hose. That could be a situation where they're not concerned about that risk.
If we could get every risk on the machine to that point, then maybe—maybe—that's not a bad thing unless you start to influence behavior significantly and the operator is taking risks they otherwise would not.
Lyons: I’d like to add from the construction site, how workers work. Kevin's correct. If you have a scissor lift that’s safe till 35 miles an hour out in the wind, the workers will start using it between gusts. Number two, I think, perhaps it's in U.S., we put together standards that shouldn't be in place. For example, we have a standard right now for working on electrical equipment that requires you to wear arc protection. What that has done is putting workers in a place where they shouldn't be because we have a standard in place.
"From the aspect of what we do or what we see as an agency, it always is going to be the responsibility of the employer to provide a safe and healthy workplace, that includes asking if the person operating the equipment was adequately trained."
—Nicholas DeJesse, Assistant Regional Administrator at the Occupational Safety and Health Administration, Region III
I think this is a great question. We have to be careful with the standards we put in place that we're not putting some of the onus on safety back onto the worker. In the case of this electrical standard NFPA, what we're saying is you can do the work but you won’t get burned “so bad.” That's very American—that's very unsafe.
Gildea: When you say putting him in a place where they shouldn't be, you're saying that the safety PPE gives you a sense of security.
Lyons: Thanks, Kevin. In the U.S., when you cut your hands, we say, “let's go up a cut level.” Instead of finding out what cuts your hands—we do PPE. Almost all the time…we focus on the worker, and protecting them versus eliminating the hazard up front. I had a guy cut his hand almost off cleaning out the inside of a duct. It was razor sharp. I called the firm up and I said, “Hey, can you deburr this?” [They said,] “Sure.” But I'm sure they yelled at that guy for not using the right gloves when we could have eliminated the hazard.
Groat: I think that design solutions are aimed at enhancing safety and reducing risk and preventing accidents, but they can lead to complacency.
I think MEWPs have increased in their efficiency and safety over the years to the point where some workers think that they're inherently safe to do whatever they want to do when they're in the equipment.
We did mention earlier, training is essential. Even with excellent design solutions, a robust safety culture is essential. If the workplace culture does not emphasize the importance of following safety procedures, users and operators might develop a sense of invincibility despite the enhanced safety measures that are in place. It's like the Swiss cheese model, that many things have to go wrong in order for an action to occur. To be reliant upon one safety device I think is an improper assessment of safe use. The risk assessment takes everything into account.
When you're looking at the task that needs to be done, that task needs to be done. If you're using a ladder, or a scaffold, or a MEWP to assist in performing that task, each one of those has its own unique hazards associated with them: climbing up and down, assembling and disassembling, moving the guard rails, not moving the guard rails. When you get to the point where you end up having this great machine that has a full guardrail platform that will elevate you to the exact height, and it has all these features that we're putting onto them, making them increasingly safe, but at the same time, it doesn't eliminate all hazards, and risk.
"Make sure that people are aware of what the overall hazards are with all the tasks that are being completed."
—Tony Groat, North American Regional Manager at the International Powered Access Federation
I think that you need to make sure that people are aware of what the overall hazards are with all the tasks that are being completed. We need to make sure that while we're talking about designing out hazards, I don't think that we can totally design them out because we have human beings being human doing sometimes stupid things.
While I appreciate TJ's perspective, which is we also can't shift safety on the backs of the operator, because they don't have control over a lot of the decisions. For me, it's like proper selection of the equipment and the MEWP is being one of them but the accessories of the MEWP are another one of them. It's the correct selection of the equipment isn't just “this model MEWP,” but it's “does it also need secondary guarding,” “does it also need all these other elements that are part of it,” “do they need a hardhat,” “do they need the gloves.” I think all of those are part of it.
Clark: I would flip that around a little bit. I feel like secondary guarding has called attention to the hazard. Now the operator is aware that there's a line or bar there. They have to put their hands in proper placement to use the machine correctly, or the disable the guarding and the machine stops. I truly believe that they're a little more aware: “Hey, there is a hazard here, I need to look at my surroundings. I need to be careful when I raise / lower / drive.”
International Powered Access Federation
Rental: Nicholas, can you speak to the dangers of complacency?
DeJesse: Tony mentioned something really good, which is there's a human element. And in that human element, , this is why we strongly encourage companies to develop robust safety health management systems. Which goes back to what was said earlier, training is foundational.
If you're building a house and you have a basement, you pour the walls and you let those walls settle. If you start building on it too soon, usually that house will fall or cave in. That's the way I've always looked at training as being the most fundamental, foundational element when it comes to setting workers up for success.
Kevin and others have mentioned the machinery, the secondary safety features and associated considerations – absolutely raises the level of awareness of what is around them [workers] or the potential for what is around them whether it is contact with an overhead line, whether that is collision warning sensors, cameras on some vehicles—not on a MEWP obviously, but some other things. All of these enhancements, , are really meant to point out and raise the level of awareness of the hazards that are in and around that area. The training aspect of it is definitely foundational.
Have we seen complacency in the past? Sure, everyone's human. That tends to occur. But this is why it's so vital as well that at the beginning of the shift, having that conversation with people out on the site to talk about, “This is what we're doing. These are the tasks of the day. How are we going to accomplish this work and ensure that no one gets hurt or gets killed? What are the safety features?”
Additionally, I think we're starting to see more employee empowerment now than we did years ago, in the form of “stop work authority.” Stop work authority comes in the form of employees saying, “that's not working out right now, something's amiss, I'm not going to force the issue, let me take a break,” call someone else, get another opinion or at least get another set of eyes on the situation. Having that stop work authority gives the employee more engagement in the safety and health process and also enables them to understand. It says, “Hey, you don't have to put yourself in danger to get a task completed. There might be another way to do it, there might be another solution.”
This connects to organizational culture--these are things that are intangible. To me, culture is the intangible. It is the collective values, beliefs, and norms of the organization. These are the things that you really focus on as an employer, that are so vital to your organization. Safety has to be one of those core values.
When safety and health is at the heart of an employer’s a core values, you shouldn't see complacency. What you'll see, is more folks engaged in the safety process, asking questions and being more inquisitive.
Groat: I would complement that, because some of these safety innovations that we talked about, you need to know how they work. You need to be able to inspect them to ensure that they're working properly, because of you depending upon them and there there's a mechanical breakdown on them – you have exposure that it's not working.
I agree 100% with the perspective that with all of innovation, with all the equipment that we have proper training and knowledge is paramount to how these things are being used. And being used properly inspected, properly maintained, all of those aspects that that are critical to the user going home at the end of the day.
More from Tony: Complacency
Design solutions aimed at enhancing safety are crucial for reducing risk and preventing accidents, but they can sometimes lead to a sense of complacency among users. This phenomenon, where increased safety features can lead to a feeling of invincibility or reduced caution, is known as "risk compensation".
If a design solution significantly improves safety, users may perceive the equipment as inherently safe, which could lead them to take more risks or neglect safety protocols. This is particularly true when safety features are highly automated or require minimal user intervention.
When users feel that design solutions have made a system extremely safe, they may become less vigilant about potential hazards. This reduction in alertness can increase the likelihood of accidents, as users may overlook risks that still exist despite the safety enhancements.
Even with excellent design solutions, a robust safety culture is essential. If the workplace culture does not emphasize the importance of following safety procedures, users/operators might develop a sense of invincibility despite the enhanced safety measures.
International Powered Access Federation
Rental: To end, I’d like to ask our primary question once again. Can we design out hazards?
Lyons: That always has to be our goal, right? If you don't design out the hazard, you have to trust that the worker will make the right decision if they have an option. I think we design out as much as we can so perhaps, they don’t have to make the decision to be safe or unsafe.
Groat: I think that it is a tool in the arsenal of safety to be implemented to ensure that the task is performed properly. But it is not the only one. It is a critical one and one that I think is the first one that we should be looking at.
But again, when you put in place, you still need to train them on how to use it properly, still need to be able to train them to recognize what the hazards are to prevent those because no single device is going to protect someone, it is a combination of many things that are required to ensure a worker safety.
Gildea: There's big improvements that can be made on the design side. It's not the only tool in the tool belt, but that's a big one. As I mentioned before, there's things going on within the design itself that maybe aren't apparent to the user, but it's there and it's moving forward. I think there are classic areas where OEMs are comfortable and experienced (electrical safety, hydraulic safety, structures, stability) and then there are other areas where improvements are made by applying new technology and by focusing on the users point of view and how the machine is used and incorporate that into the design. In any case, mitigating risk “by design” requires consistent, continuous improvement that is built into the normal machine development process.