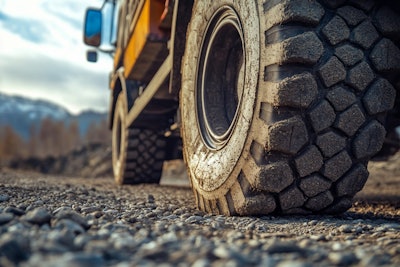
Tire maintenance is a challenge in the off-highway industry and it can keep operators and drivers up at night. Downtime is a major challenge and the costs can be exorbitant and have far-reaching effects. Phil Domm, mining tire sales manager at MAXAM Tire, offers insights on tire technology development for the off-highway industries and what the future holds.
See additional insights in his podcast interview, "When The Tire Saves the Project," broadcast in November 2024.
Question: When it comes to tire developments and technology for the off-highway industries, what has been the most interesting development the last few years?
Domm: Tire manufacturers are coming up with new ways to meet higher demands. Making tweaks to tread pattern has always been a standard procedure and part of the product improvement process, but they have to do more than that now. Part of ensuring a tire’s performance, especially at demanding mine sites where heat and cut are big factors, is the compound that goes into the tire and the technology in which creates the rubber compound. It’s a carefully crafted process that involves advanced technology and a lot of chemical science, but ultimately manufacturers can now utilize automation and create more seamless and advanced procedures in producing special compounds that go into the tires. These compounds play a big role in ensuring the tire’s performance and its ability to stand against heat and abrasion.
Question: How much of the innovation that goes into tire development comes from other industries and is there a give and take?
Domm: To break things down, tires are rubber and polymer. So, the innovation that goes into tire development ultimately is just a way to “play” with polymer, how it reacts to different jobs, applications, pressure, and others. This is a very broad approach to it of course, but polymer is used in so many things that are outside of just tires. So essentially, how we streamline the manufacturing of polymer will affect tire development. Who knows, maybe someday they will figure out how to incorporate other unthinkable ingredients to achieve a more sustainable yet effective manufacturing process for rubber.
Question: In what ways can tire selection influence fuel efficiency and load capacity in off-highway vehicles, particularly in mining or forestry operations?
Domm: Know your application; where is your application going to work in? What’s the terrain like? What pattern should you have that would maximize your ground contact? If you’re at a mine site, there’re analysis you should do to think about what the grade is like, turns, road condition, and other factors that go into the TKPH study. So, selecting the right tire with the right pattern and compound would be crucial in ensuring maximum performance for the machine.
If you’ve selected the right tire, you can’t rely on it to achieve fuel efficiency for you as tires have their limits, too. They can only carry so much and have a load capacity limit, based on the speed you’re going. Remember, high speed means more heat being generated, and heat is the biggest enemy to tires. So, if you’re going too fast, carrying too much, you’re going to decrease that tire’s life and performance regardless of the tire selection.
Question: What strategies or innovations are used to extend the lifespan of tires in harsh off-highway environments, where repairs and replacements can be logistically challenging and costly?
Domm: Manufacturers have made improvements on tread patterns that incorporate features such as stone ejectors, or self-cleaning mud breakers and what not, in addition to what we’ve discussed: The compound that goes into the tire.
However, the best way to extend the lifespan of tires is having a good maintenance plan. We can’t stress enough about this as we’ve discussed many maintenance plans. Users should:
- Do your pre-shift tire check; check the valve cap, is it leaking? Is it on? Check the air pressure, air pressure is king! Make sure you check the air pressure on a cold tire, meaning that it’s been sitting idle for at least 24 hrs.
- Train your operators: make sure they report any issues immediately, the longer you wait for the repair the more costly it’ll be, and eventually a replacement. Let them know about load capacity and speed and the proper way of loading.
- Make sure your roads are clean! If there’s spillage, make sure the clean-up crew is on it so that your operators aren’t running over large debris.
Question: What do you see as the next big development for tires and, by the same token, the biggest lesson you’ve learned thus far?
Domm: Two things to keep watch include:
- The value of proper air pressure. Low air pressure caused tires to wear fast, irregularly and in some cases leads to catastrophic failures. When tires come out of service fast due to low pressure there are additional costs to the mine site that are passed on to the consumer. There is also an environmental component. The more tires we consume the more tires are left as waste or recycled. Having a proper air pressure maintenance program and the use of a tire pressure monitoring system (TPMS) are the most important tools we have at our fingertips to extend tire life and longevity.
- Advances in rubber compounding are another tool that is coming down the pipeline in the giant mining tire world. Developing better compounding can increase our tire life, our tire performance and reduce the number of tires that the world consumes. Maxam has developed the EcoPoint3 liquid rubber mixing process. Instead of mixing the rubber components in a dry process we can now mix the various ingredients in a liquid process. This allows us to have a much finer distribution of the ingredients in the rubber compounds assuring that we can increase the needed performance goal of each rubber compound. For instance, the heat compound would handle higher heat or speed while the cut compound would have a higher tolerance to cuts, abrasions or scrub.