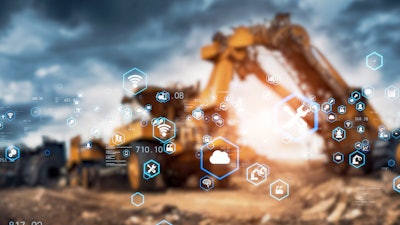
A construction site is a dynamic environment with many moving parts — heavy equipment, service trucks, attachments, and smaller tools. One equipment failure can bring everything to a halt, leading to costly delays. Running equipment until failure isn’t financially viable. To prevent unplanned downtime, contractors and fleet managers should leverage telematics data for preventive maintenance. One of the significant benefits of telematics is predicting and fixing a problem before a failure.
Challenges Without Telematics
Preventing downtime is a significant challenge for contractors, but telematics can provide a solution. Tony Papania, connectivity services territory manager of Volvo Construction Equipment, emphasized the importance of telematics in maintenance.
“Telematics are great for helping you stay on track with regular service, which is a way to prevent issues or catch them early. An advanced telematics service can also simplify the alerts you get, whereas some of the more basic versions can flood you with alerts that are not all urgent and are written with code and jargon that make it difficult to decipher and prioritize,” Papania said. “Not having or using telematics will make it harder to know about your machine’s overall health.”
Mike Kucharski, vice president of sales and marketing with Gauge, identified two major challenges companies face without telematics: limited visibility to hours and location across their entire fleet and duplicative data entry and errors. Kucharski explains that when only part of the fleet is connected, it leads to inconsistent processes and inefficient operations.
“It is wildly important to have 100% connectivity,” Kucharski said. “Additionally, it is important to have a standard operating procedure for onboarding new equipment and disposing of assets. This ensures that you can keep your information and reporting accurate and maintenance on time.”
In addition to limited visibility, Kucharski pointed out that hiring great people and retaining the ones on staff are always challenges, so using them wisely is important. “If those resources spend hours inputting and retyping data into systems multiple times, these resources are not effectively deployed. Leveraging Gauge’s professional services and vista integration framework allows employees to run at full throttle and eliminate duplicative entry,” Kucharski said.
Dave Cataldi, sales operation specialist with FleetWatcher, agreed that the main challenge for contractors who try to track maintenance and machine hours manually is simply the amount of human effort and error involved. Without telematics, field personnel must appropriately and timely log machine hours, while maintenance technicians must locate the machine in the field.
Bret Brown, associate project manager for Doran Manufacturing, underscored the critical role of telematics in tire maintenance. “Tracking tire maintenance with telematics gives drivers and maintenance teams real-time knowledge about slow leaks so their repair can be scheduled at an appropriate time that will not adversely impact safety or service — and thus avoid tire-related roadside service calls,” Brown said.
Brown believes that knowing about fast leaks or high tire temperatures allows drivers to find a safe place to pull over, which protects them and the drivers in their vicinity. “Manually tracking tire maintenance does not provide real-time information on either fast or slow leaks and typically ends in solving a problem rather than avoiding one with telematics,” Brown said.
How to Manage Telematics Data
Effectively managing telematics data is essential since specific data points are crucial. Also, one consideration is whether notifications about abnormal data should be a priority.
Papania believes more advanced telematics services are helpful when managing all the data. “The number of alerts can be overwhelming, ranging from low wiper fluid to major engine issues. If the alerts are not clear and concise, you’ll have to dig through them to make sense of it all. For example, Volvo’s advanced telematics system, ActiveCare Direct, prioritizes fault codes by how critical they are and sends only the ones that need attention right away. An alert plainly states what the issue is, how to resolve it, and what the consequences could be if it is not resolved. The manager can go in later and look at any other alerts that should be addressed when they have time,” Papania said.
Kucharski recommends focusing on what’s important and diving deep into equipment that shows up on your maintenance schedule. “With Gauge, we provide the user with the ability to create automated reports and personalized notifications via email or text when their parameters are met. This allows users to focus on their work and not log into a system every day,” Kucharski said.
Cataldi notes that FleetWatcher works closely with contractors during implementation to ensure they can easily find the data and reports most relevant to them. “Throughout their time as a FleetWatcher customer, we set up scheduled check-ins with the contractor to address any data or reports that look abnormal or that need to be addressed. As the contractor and their team get more familiar with the system, they can often address any anomaly on their own,” Cataldi said.
Brown explains that Doran tire monitoring systems provide pressure and temperature data on all connected tires within the fleet. “This allows drivers and maintenance personnel to monitor slow leaks so that they can be dealt with in a safe, timely, and efficient manner. Fast leaks and high-temperature alerts require immediate action by the driver–namely finding a safe place to pull over so that tires can cool down or crews can change a flat in a safe area,” said Brown.
Operators can schedule repairs that eliminate tire-related roadside breakdowns by learning of a slow leak in advance.@Dmitry - adobe.stock.com
Receiving Alerts for Abnormal Operating Conditions
A crucial aspect of telematics is the ability to receive timely alerts for abnormal operating conditions, which keeps users informed about what’s happening on the job site. Cataldi emphasizes the importance of these alerts. “They give contractors immediate notification of any operational issue that might cause a production slowdown, affect the functionality or depreciation of an asset, or reduce the project’s margin,” Cataldi said.
Papania adds that fleet managers typically receive notifications about abnormal operating conditions based on the telematics platform but often receive them via mobile phone notifications. “A monthly report can also be emailed to show utilization trends, maintenance needs, and lower-priority alerts. We also have an uptime team constantly looking through fault codes on the customers’ behalf and looping in dealers when appropriate,” Papania said.
Brown said Doran systems feature a patented “green means good” display, which allows the driver to tell at a glance if there is an issue with one of their tires. “When pressure falls below normal operating conditions, an audio and visual alert is triggered for drivers and maintenance personnel. Audible tone and a 'hot' warning for the tire in question are indicated if a tire temperature exceeds 175 degrees Fahrenheit,” Brown said.
Examples of Telematics Preventing Downtime
Beyond alerts, telematics plays a key role in preventing downtime by identifying issues before they become critical.
Papania shares that common issues flagged by telematics include:
- High-speed shifts on wheel loaders
- Using the wrong work modes on excavators
- Overuse of differential lock engagement on articulated haulers
“When telematics flag these, the owner or fleet manager can identify potential training needs,” Kucharski said. “Ultimately, any adjustment that can reduce wear and tear will help lower costs and increase uptime.”
Kucharski believes the biggest opportunity to prevent downtime is with Gauge’s Mobile Service Request feature. “Gauge enables the operators and foreman to highlight needs that may be important but not urgent. This allows the equipment manager to align the request with a planned maintenance schedule, saving downtime, travel time, and ordering parts proactive so that the repair can be completed at the same time as the scheduled maintenance.”
Cataldi points out that the FleetWatcher system provides up-to-the-minute engine run-time and idle-time data. “A contractor can easily notice when an asset has been excessively idling and not productive on a project or if there is a backup at a loading or unloading location. This can all be seen via an alert or report on mobile, tablet, or desktop,” said Cataldi.
Brown explains that customers routinely tell them they can schedule repairs that eliminate tire-related roadside breakdowns by learning of a slow leak in advance. “That is especially important for customers like ready-mix concrete companies and others hauling perishable loads. These customers have reported eliminating ‘run flats,’ which are dangerous, and greatly reducing tire-related roadside service events, which increases customer service and eliminates the waste of a ruined perishable load,” Brown said.
Tire monitoring through telematics enhances safety, lengthens the service life of tires, saves tire casings, and reduces costs.@AvokadoStudio - adobe.stock.com
Advancing With Telematics
The construction industry is increasingly driven by data and technology, making telematics important for businesses.
Kucharski points out that while some companies may have maintenance software and others may have telematics solutions, the key is finding the right fit for your needs, no matter where you are on your journey.
Cataldi added that telematics aims to track the location of assets and, more importantly, understand how they are being used. “That real-time usage data can quickly inform a contractor of how on track or behind they are on a project and what they can do about it,” Cataldi said.
Brown highlighted the significant benefits of adopting automated tire pressure and temperature monitoring through telematics. This enhances safety, elongates the service life of tires, saves tire casings, and reduces costs by eliminating (or significantly reducing) tire-related breakdowns, which improves customer service with on-time deliveries. “A wide range of options are available to suit fleets of all types and sizes, as well as off-road equipment,” said Brown.
Papania noted that embracing these technological changes is crucial to keeping up with the competition and setting the pace. “It may seem challenging, but in most scenarios, the benefits far outweigh the risks,” said Papania. “Your dealer and/or OEM should be able to train you on the software to a point that makes it more comfortable and intuitive.”
Read Moreeqtoday.co/r4y0wl53
Julie Smith is a freelance writer for Equipment Today.