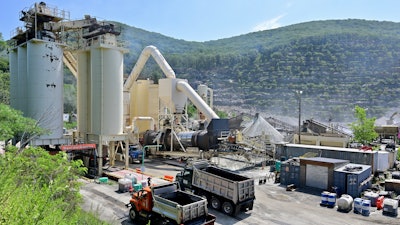
It's not uncommon in the northern parts of the country, for asphalt plants to perform their regularly scheduled maintenance and upgrades during the colder winter months when road construction and maintenance aren't active. The work of producing asphalt takes a heavy toll on the various systems and moving parts of a plant, and reinvesting in the replacement of older components while your intentionally shut down can make a world of difference in reducing downtime when you're at the height of the season.
While this might seem like common sense to most, it's surprising how many people in the industry I talk to who relay various stories about lack-luster maintenance programs or only surface level fixes. While it's not the ideal way to operate, placing the proverbial band-aid on wear-and-tear issues, it can happen more often in tighter or uncertain economic environments. However, one company's proactive approach to their plant upgrades shows why playing the waiting game usually backfires in the end, even if it saves on short-term costs.
Best To Have A Plan
Thalle Industries
Joe Klein has been the plant manager at the Thalle Industries in Fishkill, NY, for the previous seven years. In that time, he says, it's been standard practice to target and take action on plant improvements during their offseason. It's baked into their annual plans.
Thalle has existed in one form or another since the founding of Thalle Construction in 1947 by Guido Pacchiana, the grandfather of current CEO Glenn Pacchiana. It became Thalle Industries in 1985 under his leadership, and continues today. That kind of longevity doesn't happen by accident, it's baked into the way they do things.
"We don't want to have downtime," said Klein. "Each winter, everything is planned out in advance. We replace what needs to be replaced, and we don't wait around for it to break.
The plant he manages regularly sees up to 350 tons of asphalt per hour head out of its gates, as they produce for a wide variety of contractors and their various needs in the area. Downtime is their biggest enemy, and avoiding preventable breakdowns is what drives their continued investment and careful attention.
"If we have downtime, we won't be able to provide what someone needs when they need it, so we have to have a plan every winter about what we are going to fix," said Klein. "One of our biggest headaches, believe or not, is that we can sometimes get too busy, and that can become a problem. A plant can only make so much asphalt in a day. It always works out that everybody is scheduled at the same time, you know."
The worst case scenario for these extremely busy schedules, is to have a lineup of customers all ready for asphalt, and for a serious breakdown to occur that could have been prevented.
What Makes A Huge Difference
Thalle Industries
Ahead of the 2024 season Thalle decided to make two new upgrades to their plant. The first was to their baghouse system. To do that, they decided to go with the Meeker designed Freedom Reverse Air Baghouse.
This design removes the need for solenoid valves and the need for an air compressor. With a unique control of its turrets, it provides improved control over the return of fines to the drum, extends the overall lifespan.
"It's a much more consistent product," explained Klein. "When you think about it, it's just a way to return dust back into your mix without putting it into the atmosphere, but it makes it more consistent."
In a press release shared earlier this year, president and CEO Glenn Pacchiana said, "Air quality is one of our top priorities, and the new baghouse ensures that we meet all our obligations."
Klein continued, "the [baghouse] we had before worked great too, but these things wear out. We burn fuel, it gets sent through, things rust. It's part of the plant that is heated to over 280 degrees and then is cooled down in the evening every day. It builds up moisture. The [Meeker] is probably biggest, most powerful baghouse we could have got. It's very efficient."
[MEEKER QUOTES]
Thalle Industries
The second offseason upgrade that Thalle proactively invested in was a brand new, ultra efficient Astec Heatec hot oil system.
"It's a much cleaner burning version, that's why we got it," said Klein. 'It's ultra-low NOX, which is one main reason we got it. It's much more efficient. Also, another big reason was just the way it works is just a lot simpler [than what it replaced]."
The Heatec heaters are built around a helical coil, an extremely efficient (up to 85% LHV) and reliable design, and they're also versatile enough to be used for a number of different applications. Increasing efficiency reduces fuel usage, which, in turn reduces costs.
They come in two basic configurations: HCS (single circuit heater) and HC (multi-circuit heater). The HC model has a manifold and side pumps that enable the heater to operate up to four hot oil circuits. The HCS is better suited for situations where are not a lot of components in the circuit.
Klein expressed a high degree of satisfaction working with both companies during and through the installation process.
"Both Astec and Meeker do a phenomenal job," He said. "They handled everything with the install, and they kept all their deadlines. They both were easy to work with, and had the great ability to say when they were going to be there, and then getting the job done on schedule."
That's important for their region, because the weather can be really unpredictable and make things suddenly very difficult to work in.
Thalle Industries
"We try to do it where we have everything ordered and ready to go pretty early. We want to be we want to be ready for it, because we only have a couple months to do it," explained Klein.
"Working in New York, the Upper East Coast, it's much harder to depend on the weather to cooperate. The biggest thing is having everything set in stone ready to go. We can have cranes ready to go on site, but you know, if it starts snowing, you're not using a crane. Sometimes it's not cold enough, so it'll rain, and that makes it dangerous, so you have to take precautions."
In the future, Thalle Industries plans to add some more Astec long term storage tanks, like the Heatec Thermo-Guard series.
"We have two of those silos already, and we can store material with them up to four days," said Klein. "When you consider fuel costs, liquid [AC] and starting up and shutting down this plant, the fact that you could fill these silos up and just shut the place off; and you could store the material and come back in the next day without having to worry about it. It's a big deal. There's no waste; everything you made is sold."
Thalle Industries
More Than You Bargained For
As improvements and/or replacements are made, however, it's not just the new component itself that you're getting with the purchase. While new technology, features, and other bells-and-whistles are all great, there's another significant reason to consider regularly investing in new equipment.
As time progresses, older models and machinery require more and more maintenance as they age, but it can become harder and harder to find the necessary parts for them. As older forms of technology become obsolete, supplanted by newer iterations, the supply of repair materials can become gradually more scarce.
"When you get new equipment, it's much easier for us to get spare parts or do maintenance, and keep the plant going," said Klein. "The new equipment keeps us from having downtime. So when there's a job that might be an emergency, you know, an immediate issue that has to be fixed, like they can depend that we're going to be able run."
Thalle Industries
Such was the case on July 9, 2023, when major storms poured eight inches of rain overnight, causing significant damages to Bear Mountain State Park and Route 9W in Fort Montgomery and other parts of the Hudson Valley -- the region where Thalle Industries has been the go-to supplier for such emergencies for a long time.
In a statement released at the time, Pacchiana commended his employees for their extra efforts.
“Our employees at our Fishkill quarry and asphalt plant [started] their shifts earlier and [worked] later to accommodate orders for rock and asphalt to restore damaged roads,” he said. “We pride ourselves on quick response times for clients, so we are able to respond to emergency requests within a few hours.”
Thalle responded to an emergency request for Route 35, where a water-main break damaged and closed the major thoroughfare in Yorktown. With an emergency delivery of twenty-two tons of asphalt from the Fishkill location, the road reopened in less than a day.
Pacchiana credits the company's growth and success over the decades to their "rock-star" employees, and Thalle has a reputation for supporting the growth and well being of their workers both in and outside the workplace.
Thalle Industries
"I’m a big believer in professional and personal development, so Thalle helps employees learn about and develop themselves by providing resources in executive coaching, leadership courses, industry councils/training, computer skills classes, and health and financial wellness initiatives,” said Pacchiana.
Klein echoed these sentiments. "It's not some huge [anonymous] corporation, you know, it's a lot more family friendly. We all work well together, everyone gets along, and nobody is really a stranger."