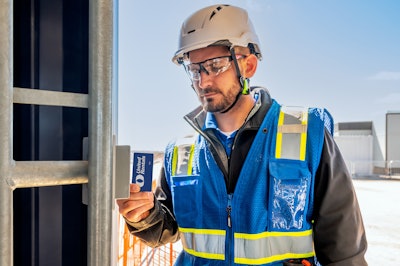
Digital technology is poised to revolutionize construction jobsites, making them smarter, safer and more efficient. One aspect of daily operations ripe for improvement is access management.
On large, busy jobsites, managing site access is essential to the safety and protection of people and property. A secure jobsite perimeter is the first line of defense against accidents and other incidents involving trespassers and against vandalism and theft. Restricting access to potentially hazardous buildings, areas and zones is equally important to minimizing risk, as safety managers well know.
While most large contractors use some method of site access control, fewer companies currently invest in a method of equipment access management, despite the many benefits of keeping unauthorized personnel off aerial lifts, forklifts, excavators and other heavy equipment.
Digital tools that facilitate both jobsite management and equipment access management also streamline access control and provide increased visibility and accountability. RFID badges are “key” to a scalable, streamlined solution.
Managing Jobsite Entry & Exit
For decades, jobsite access management consisted of paper sign-in sheets at guard stations. Lining up to sign in created congestion and delays, and people who were determined to sneak past these checkpoints could often find a way. Modern methods that use software and hardware to automate access control represent a leap forward.
Many of these systems use company-issued ID badges, fobs or other credentials to authenticate entrants based on worker profiles stored in a software platform. The profile may contain only basic information, such as name, badge number, company, and trade or craft, or additional information such as operator certification and training. Companies can assign roles and rights based on this data during onboarding.
Badges may be enabled with a magnetic stripe, barcode or RFID tag, but RFID technology has distinct advantages. RFID tags can store more data than magnetic stripes. RFID readers can read multiple tags at once, unlike barcode readers, and they can read badges from a greater distance than previous technologies.
At jobsite entrances, including gates and vehicle access points, authorized workers tap their badges on RFID readers for access. Additional readers may be placed in strategic places on the jobsite to control access to specific buildings or areas.
Smart turnstiles equipped with RFID readers take site access control to the next level. Modular units integrate easily with perimeter fencing. Security cameras and facial recognition software can be added as part of a comprehensive site security program.
Controlling Access to Equipment
Inappropriate use of equipment is a leading cause of construction equipment accidents. Workers who lack the proper training and certification are more likely to misuse equipment and cause an accident that results in injury to themselves, injury to workers on foot or damage to the equipment and nearby structures.
Keeping unauthorized operators, including untrained workers and unauthorized subcontractors, off equipment not only reduces accident risks but also helps protect companies against liability.
Keypad ignition locks that require a PIN are one effective solution. Ideally, managers assign a unique PIN to each individual operator to prevent PIN sharing and track machine usage by operator. A next-generation approach that saves time and effort uses RFID readers added to the equipment locks. Rather than entering a code, workers tap their badges for access to equipment they are authorized to operate.
Companies can assign equipment access privileges by trade, group or individual for specific pieces of equipment or equipment category classes. If a person’s privileges need to be revoked for any reason, changing the rights assigned in the worker profile restricts access immediately.
A badge approach to equipment access control provides accurate real-time and historical insights into equipment utilization. Worker-specific utilization data increases accountability in the event of an accident or equipment damage. It can also help companies identify authorized operators who may need additional safety training.
Automation Drives Productivity & Efficiency
Digital tools automate processes, potentially resulting in significant labor efficiencies and productivity gains.
For example, badge-based jobsite access reduces the need for security personnel at entry points and frees up guards to focus on other tasks, such as inspecting bags. Badge-based equipment access relieves administrators from the time-consuming task of assigning PINs for each piece of equipment and each authorized operator.
Attendance data is automatically generated and instantly accessible so supervisors and project managers can monitor workforce presence and verify worker hours for payroll purposes. Historical data on hours spent on the jobsite by different trades and crafts can help managers optimize workforce utilization and scheduling. Accurate records of worker hours, breaks and overtime can aid in compliance with contracts and labor regulations.
Should an accident or a jobsite emergency such as a fire or hurricane occur, clear visibility into who is on site and who is in a specific building or area can facilitate a faster, more effective emergency response. Managers can easily access worker profiles to obtain emergency contact information if needed.
Looking to the Future of Access Management
As projects grow larger and more complex, access management is becoming an even more critical component of jobsite safety, security and productivity. A jobsite that’s connected from end to end gives large construction companies unprecedented visibility into, and control over, who passes through jobsite barriers, enters sensitive or restricted areas and operates equipment, all while driving tangible improvements in efficiency and productivity.
In the foreseeable future, a truly seamless solution will leverage one cloud-based software platform to connect jobsite access management and equipment access management and allow the same worker profile and ID badge to serve both purposes. In the meantime, one-stop-shop rental companies can help general contractors evaluate access management approaches and choose tools that work best for the project, the jobsite and the budget.