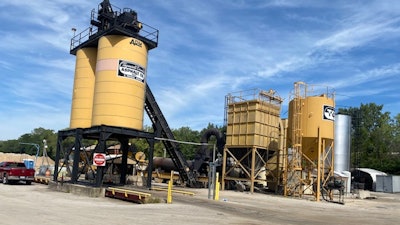
Before he passed away, my grandfather used to say, "Machines are meant to run." He spent his life working as a mechanic for several factories and metal shops in Northeast Ohio, and, eventually, he ended his career working at NASA's Glenn Research Center in Cleveland.
He basically had a full machine shop in his garage, and, when I was a teenager, every winter he would tell me to bring my car over so we could check out how well it was doing what it was supposed to do: run. While I believe this basic tenet holds true, it runs into a snag when it comes to the asphalt industry.
For many across the United States, the winter months mean shutdown. In places where it gets particularly cold and have heavy amounts of snowfall, there's not a lot of asphalt going down during that time. This results in the machines you rely on for you business and your livelihood aren't doing what they were meant to do. They aren't running, they're sitting cold.
Another thing my grandfather believed was that, somehow, when machines sit cold for awhile they don't always want to start back up the same. At Tazewell County Asphalt Company in Perioira, IL, they have developed strategies to deal with the downtime, and ensure their spring start-up doesn't get hit with major setbacks.
Backstory
Born in 1937, Carl Kaufman Sr. founded the company in 1976, and still comes to work every day even with his kids and their children now handling the majority of the on-the-ground operations. The now third generation company started out paving and doing other asphalt work before buying their first plant in the late 1990s, and then recently expanded their reach by purchasing McLean County Asphalt. This brought their service area to just about all of Peoria and Bloomington, Illinois.
The 100% union operation, with about one hundred employees between the two company arms, has crews for sealcoating, paving, three milling machines, crushing, recycling, and, of course, their ADM asphalt plant.
"It's kind of a mix of a few different components, but the heart of it is an ADM," said Brandon Fogler, VP of operations at Tazewell Asphalt. "We always have an [offseason] maintenance plan, as well as things we need to take care of before the spring gets here. The goal is, obviously, to avoid any significant downtime during your busy season. You want that to go as smoothly as it can."
Part of the pre-season routine that Tazewell prioritizes each year:
- Maintenance Scales
- Change Gear Box Oils
- Turn Conveyors
- Inspect/Replace Belts
- Calibrate Dry Feed Bins
- Replace Filters
- Inspect Chains
The drag conveyor was a component that they highlighted as of particular importance, working hard every day to pull the material up into the hoppers before unloading into trucks. It can stretch, deform, and thin-out over time, and sometimes faster and in fewer years depending on the production loads in a given season.
"They literally go out there with a micrometer and a tape measure to see how far it has stretched, and we will call the manufacturer to see if it needs to be replaced [before the season]," said Fogler.
It's not something you can afford to replace midseason. The goal of all these checks and measures is to ensure the best possible chance to avoid major malfunctions or downtimes. If something is questionable, if they can't be certain it will last the full season, then it has to get replaced or serviced to start the season on a fresh slate.
"We treat it [the plant], maintenance wise, just like we would a paver, a backhoe, truck, or anything else that's down for the winter," said Carl Kaufman. "You have a list of things and you make your way through it, changing filters, oil, inspect chains and supply lines, belts, and you stay ahead of it."
A Costly Contrast
One timely illustration of the importance of these types of maintenance plans came in the aftermath of the purchase of their second asphalt plant.
Every year, as part of Tazewell's maintenance plans, they make sure to take the time to drain the liquid asphalt tanks, inspect them for excess deposits or buildup, and clean them as necessary. However, after having taken over the maintenance at the second location, there was found an issue that required an expensive fix.
"The bulk storage tanks [at McLean] for the liquid asphalt needed to be cleaned out pretty [significantly]," said Fogler. "There are hot oil lines that run along the bottom of those tanks about a foot off the [ground] and they cook the material at about three hundred degrees. They cook and they cook, and time passes and it cooks some more. Then you get to a point where it's the worst [we've] ever seen."
After having an expert come and review the situation, the buildup was so severe that meant tens of thousands of dollars in repair work for the two tanks.
"It was hard as a rock," said Fogler. "Now, they have to go in there during the winter, with it all froze up, and literally chip it out with hammers. They scoop it out with buckets and throw it out of the little man-door. When they get down near the bottom, in order to not pierce the pipes full of hot oil, they have to blast the buildup with dry ice."
Folger explained that once this repair is completed, they expect a massive return in proper heating efficiency once the spring rush is in full swing.
"By not having to heat up this huge block of burned-on asphalt, we should get a ridiculous amount of efficiency brought back to us," he said.
With natural gas prices hovering around a national average of $4 per Metric Million British Thermal Unit (MMBtu), the dollars can add up quickly over the course of an entire season, if you are needlessly compensating for caked up, old liquid asphalt.
"It's like a well insulated house, right," explained Fogler. "If you want to get ten-to-twenty thousand gallons up to three hundred degrees, and you're trying to heat it through a solid block of caked on AC, you're not going to be very efficient. But if that oil and material can flow around the pipes and tank evenly, it's going to cost you less.
The State Certification Process
Not every asphalt plant has to concern themselves with it, but for those who are supplying to the Department of Transportation (DOT) or even cities or municipalities that utilize a DOT spec mix design, then you have to go through a detailed and lengthy testing process to ensure you are meeting not just a quality standard, but a consistent operational process, as well.
"If you're just going to do driveways and maybe parking lots somewhere, you don't have to be state certified," said Fogler, as he explained some of the various calibration tests that a representative of the DOT must come out and make in-person.
The first calibration test focuses on the actual cold feed bins. The state auditor provides certain mix-design requirements which the plant must then produce on command, consistently, and repeatedly demonstrating that each bin is accurately supplying the correct materials in the correct quantities for the spec.
"They run all the materials through dry," said Fogler, noting that they have to do the tests over multiple days. "You show them that you can put 20% sand, 50% rock, 6% oil, or whatever your quality control lab calls for, then the State looks at it and run their own tests. Then they run each bin individually, including the oil into like a pot, and you do it over and over again to hone it into a spec. It can take a couple days, but once you get all the bins calibrated to produce the result you want for each, then they'll certify."
Because of the time consuming nature of the testing, Folger noted that it's usually something they take care of in the earliest parts of the spring, or as soon as the weather allows.